
Chemical Injection Pumps in the Oil and Gas Industry
The Upstream, Midstream and Downstream Oil & Gas companies are always looking to:
-
improve production capacities
-
optimize production processes
-
assure flow performance
-
protect infrastructure
-
and reduce downtime

One simple and efficient solution is to inject chemicals into the processes, to increase the production capacity, inhibit deposits, reduce the corrosion, and make the process more reliable. These chemical injection systems are largely used in the O&G production sites to prevent and mitigate some problems that might negatively impact the process.
Upstream: Industrial Water Treatment in O&G
-
The Upstream O&G operators use the secondary and tertiary extraction processes to treat large amounts of produced water to discharge or reinject into the crude oil or gas reservoirs. They inject chemicals such as nitrate inhibitor, (sodium) hypochlorites, deoilers, antifoam agents, biocides, solvents, solids inhibitors, emulsifiers, coagulants and flocculants for clarification, recovery and sludge dewatering.

Injection pumping package in small footprint
Meeting Production Demands:
-
Examples that adjust the production rates to the market demand:
Production flexibility can be reached by using the metering pumps compliant with the API 675 standard which have an integrated flow adjustment feature to vary the flow rates within a ratio 10:1 (or higher ratio), in order to modulate the production

Injection package with integrated instrumentation and tanks
Upstream: Well Production in O&G
-
Examples that increase the well production capacity:
The natural gas extraction processes use metering pumps to control hydrate formation by injecting hydrate inhibitors (methanol, glycol, MEG, anti-agglomerate LDHI/paraffin/corrosion inhibitor). Upstream O&G companies inject scale inhibitors, anti-foamers, and wax inhibitors into the pipeline to meet the flow assurance requirement.
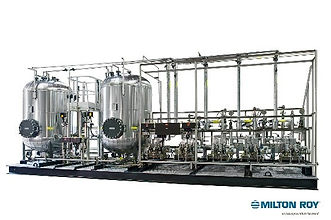
Injection package with integrated instrumentation and tanks
Example: to minimize the production installation downtime, to protect and prolong the lifetime of pipelines and process equipment by hindering agents that can create failure modes. Upstream O&G companies mainly use the metering pump to inject corrosion inhibitors, H2S scavengers, demulsifiers, foam inhibitors, and biocides to protect the topside equipment and injection wells equipment.

Methanol Injection Package
Midstream: Pipeline Oil Flow Efficiency
Example to improve the oil flowing efficiency along the pipelines:
The Midstream O&G transportation companies use metering pumps to inject some diluents and Drag Reducer Agents (DRA) at strategic points along a pipeline network to reduce turbulence and optimize flow efficiency.

Triplex Primeroyal Package
Downstream Injection Application:
Examples to make the process more reliable :
Dosing emulsion breakers (demulsifiers) into the crude oil/water separation application, dosing antifoaming agent into the gas sweetening process.

Chemical Injection Package - Oxygen Scavenger Application
DWS offers a wide range of pumps with a large choice of equipment and material options which could be configured for any chemical injection application.

Primeroyal Series of Chemical Metering Pumps
DWS API 675 pumps are the most advanced metering pumps dedicated to chemical injection systems/packages, because of the flexible modular drive design combined with the packed plunger or the high-performance diaphragm liquid ends. The modular design enables multiplexing and customizable configurations to maximize performance in a small footprint.
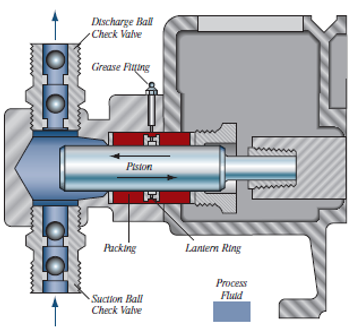

Cutaway view of packed plunger and metallic diaphragm Liquid End
Some chemical fluids, like methanol, require a leakproof design because the methanol fluid is volatile and dangerous for people and the environment. Milton Roy recommends the use of double diaphragms combined with a diaphragm rupture detection system to optimize the safety of this critical application.
The PTFE or metallic double diaphragm is designed to inject continuously or intermittently the methanol at high discharge pressure, up to 1034 bar (15.000 psi) in standard, and 1379 bar (20.000 psi) on demand.
DWS designed innovative features to improve the efficiency of chemical metering pumps, such as the patented DSD technology (Dynamic Stiffness Diaphragm) which is used for dosing viscous chemical products, at low flow rates and high discharge pressures.
The patented internal MARS pilot valve (Mechanically Actuated Refill System) combined with the internal pressure relief valve is a proven technology to increase the reliability of the pump, in case of unexpected running conditions and to prolong its lifetime.

Cutaway view of packed plunger and metallic diaphragm Liquid End
The innovative variable eccentric drive combined with proven experience in metering pump technology gives the highest reliability in most chemical dosing processes with high repeatable accuracy. This variable eccentric drive design gives flexibility of production, by modulating the flow rates during the operation.
DWS metering pumps have been used in hundreds of installations worldwide with one of the best reliability track records.
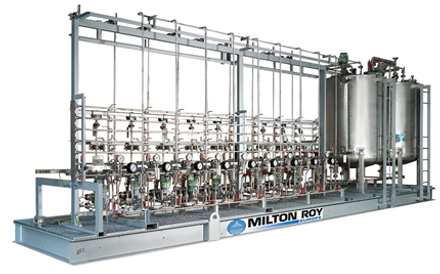

Variable Eccentric Mechanical Drive
mRoy pumps using actuators to control the flow variation in gas applications